“The SeaChange Risk Awareness System made the risk assessment process easier and SeaChange connected our people to the safety message through their visual risk communication training tools – our Health and Safety standards have increased as a result.”
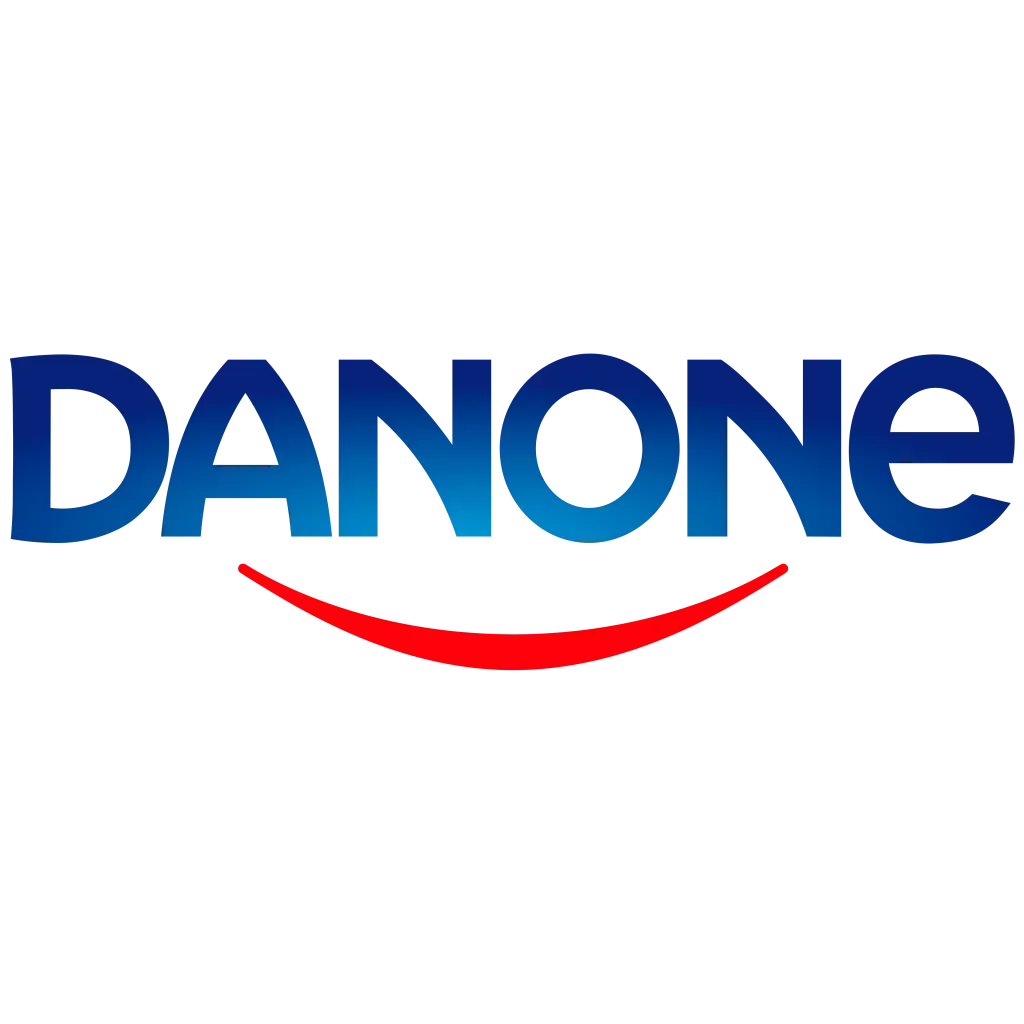
Danone Wexford
Danone Wexford became a Global Safety Leader through SeaChange Solutions
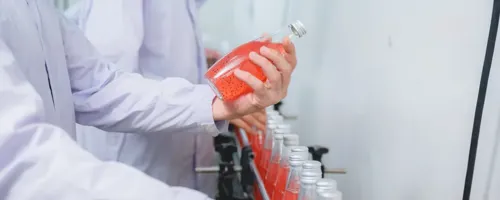
Client Profile
Danone Wexford is an independent manufacturing plant and part of the Danone Global Group, a world-leading food and drink company built on three businesses: Essential Dairy and Plant-Based Products, Specialised Nutrition, and Waters.
The Challenge
The senior leadership team at Danone Wexford realised that there was a problem: despite existing safety systems and resources in place, the site was still having accidents, incidents, and demonstrating unsafe behaviours.
Something was missing; there was a safety culture gap between what management experienced and the operational reality on the ground. Danone Wexford found the missing piece in the form of SeaChange.
The Solution
In an effort to close the safety culture gap in their manufacturing plant, the senior leadership team at Danone Wexford began searching for Safety Culture expertise. They noticed that, while most safety consultants provided information on ‘what’ the problem might be, SeaChange provided the ‘how’ to fix it. They chose SeaChange as their Safety Culture Partner because they recognised that SeaChange Solutions would help to connect safe behaviours and personal accountability to their existing safety systems and bridge the safety gap.
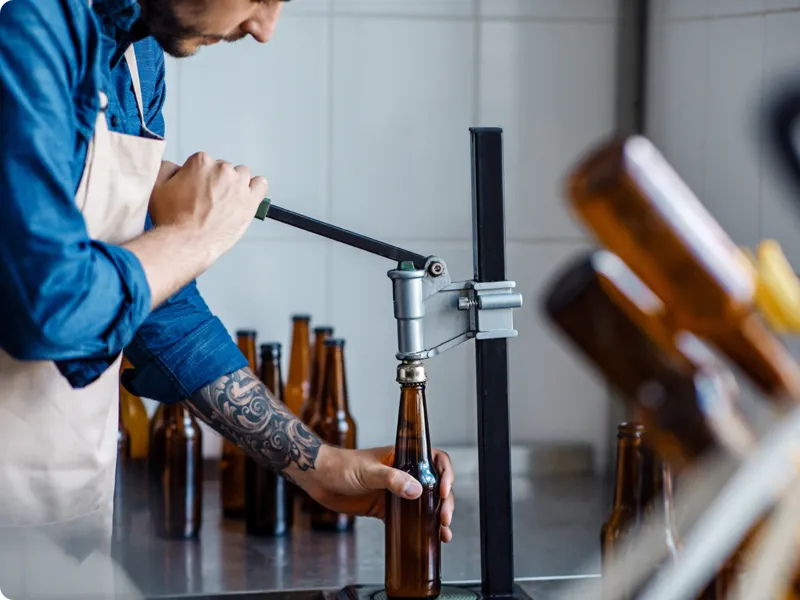
Phase 1: Measure Safety Culture to Identify Gaps
The first phase was to accurately measure the safety culture onsite and identify problematic behavioural and cultural gaps. SeaChange completed Safety Culture Footprint workshops with a 20% sampling of the workforce across all levels within the organisation. These engaging workshops enabled SeaChange to gather and analyse valuable information on the prevalent attitudes, behaviours and operator frustrations that were creating the lack of ownership for safety on the ground. The Safety Culture Footprint process resulted in a report that accurately measured Safety Culture and prioritised key actions required to make immediate improvements.
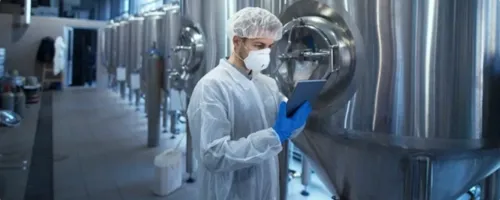
Phase 2: Implement Safety Systems
The second phase involved implementing a behaviour-based solution that would increase personal accountability and staff ownership from the ground up. SeaChange introduced two systems to Danone Wexford, designed to complement, not replace, the existing systems onsite.
These systems were as follows:
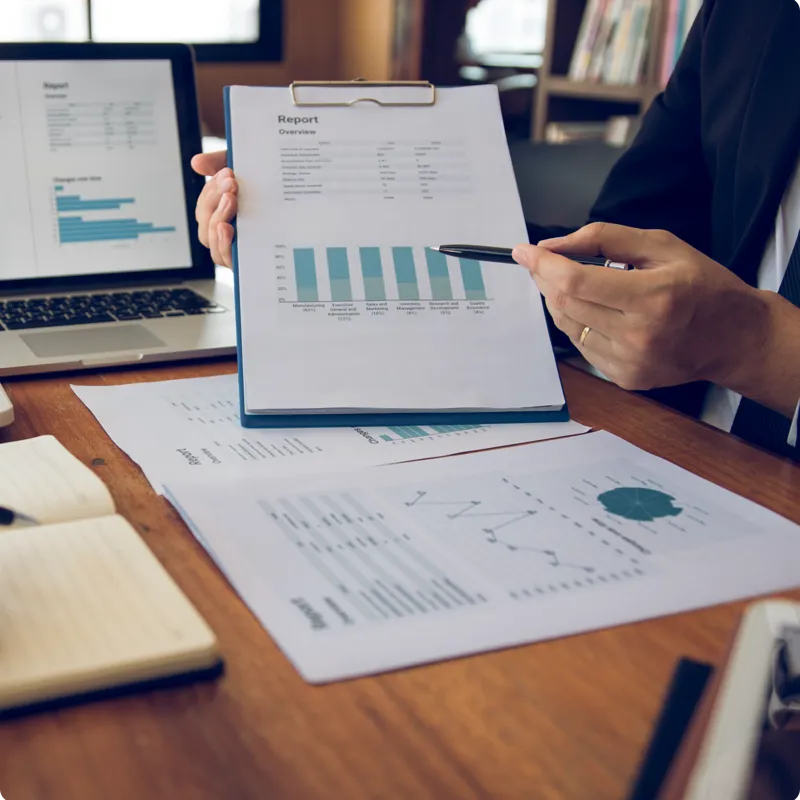
Risk Awareness System
This system enabled Danone to engage with their workforce and create visual safety standards, known as Job Safety Awareness (JSA©) visuals, for local areas of operation throughout the factory. These visual tools helped to animate risk, hazards and controls while also ensuring that the workforce was trained and refreshed in key safety standards. This system served to bring ‘safety to life’ on the factory floor.
Safety Ownership System
This system was introduced to improve local safety ownership through effective risk prioritisation and safety actions across the factory. Safety Action Teams (SAT©) were established across numerous zones within the factory. These SAT teams managed the risk priorities across shift patterns in their local area through an interactive SAT display in each zone. Local SAT teams included operators, a team leader and the front-line managers, with each individual playing a part in identifying risk priorities and actioning safety behaviours. This key process began rebuilding a safety culture from the ground up.
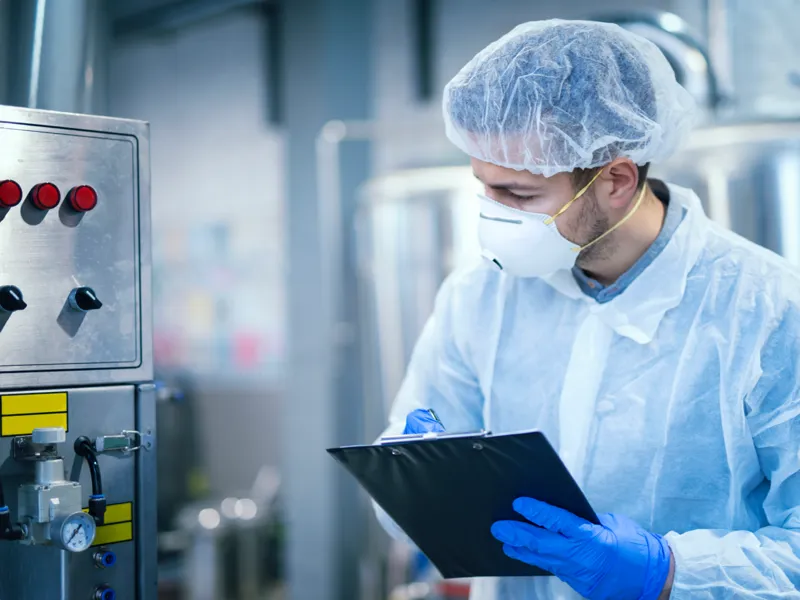
Phase 3: Leading Safety Culture in a Sustainable Way
In the third phase, SeaChange provided Safety Leadership Training and Coaching to Front Line Managers through the Zenith Leadership programme. This FLM leadership coaching helped to deliver consistency within the SeaChange systems and the wider safety culture programme, and it ensured long-term sustainability. Regular status evaluations provided leading safety indicators (as opposed to lagging) to the senior leadership at Danone Wexford. This meant that potential incidents and accidents were being prevented ahead of time. The SeaChange KPIs sat perfectly alongside existing site KPIs, ensuring the safety culture shift remained sustainable, real and continuously improving.
The Result
To date in Danone Wexford there has been a huge safety culture shift, from apathy and hopelessness to people feeling connected and taking ownership of safety standards across the factory. The workforce is now getting involved and making a difference. The safety culture in Danone Wexford has significantly evolved and SeaChange Systems are evident on the factory floor through visual tools and interactive displays.
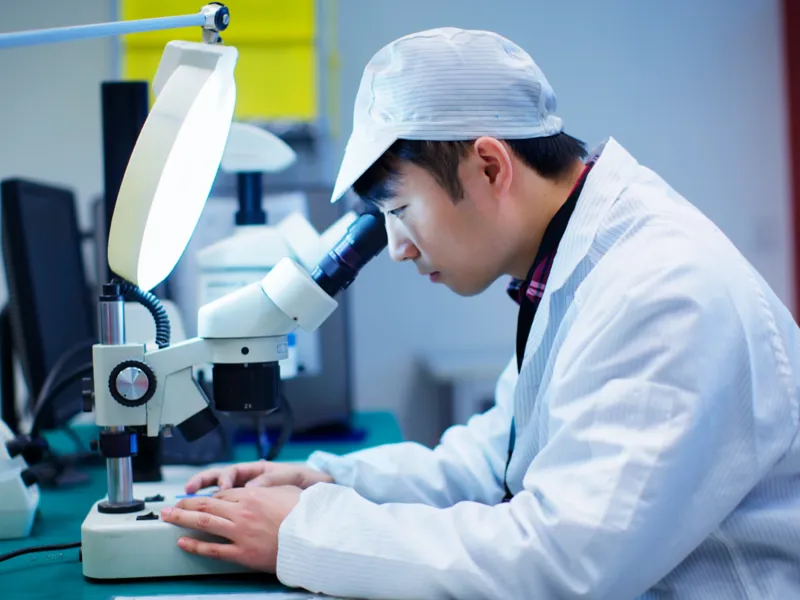
At Danone Wexford, the safety culture has advanced from a reactive response to a proactive approach, that not only manages risk but promotes safe behaviours across local areas of operation. The workforce is engaged and empowered to manage safety in a real and sustainable way. Since employing SeaChange to improve their Safety Culture, Danone Wexford have seen:
-
80% increase in workforce engagement
-
50% decrease in lost time incidents
-
83% increase in their Global Safety Audit Scores within the Danone Group
These market-leading results are clear indicators that Danone Wexford have found the missing piece in building a sustainable safety culture – SeaChange
Liam Carmody | Site Director, Danone Wexford
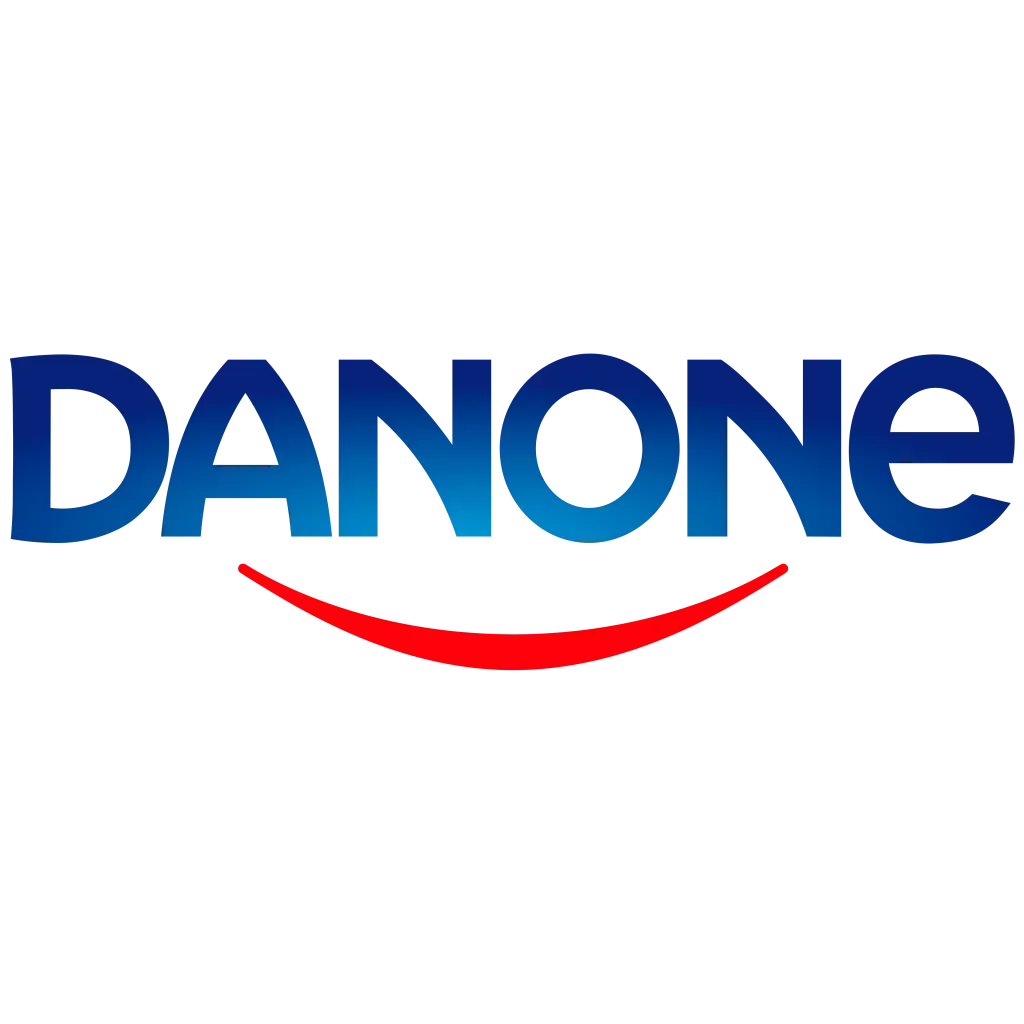
Case Studies
Trusted By
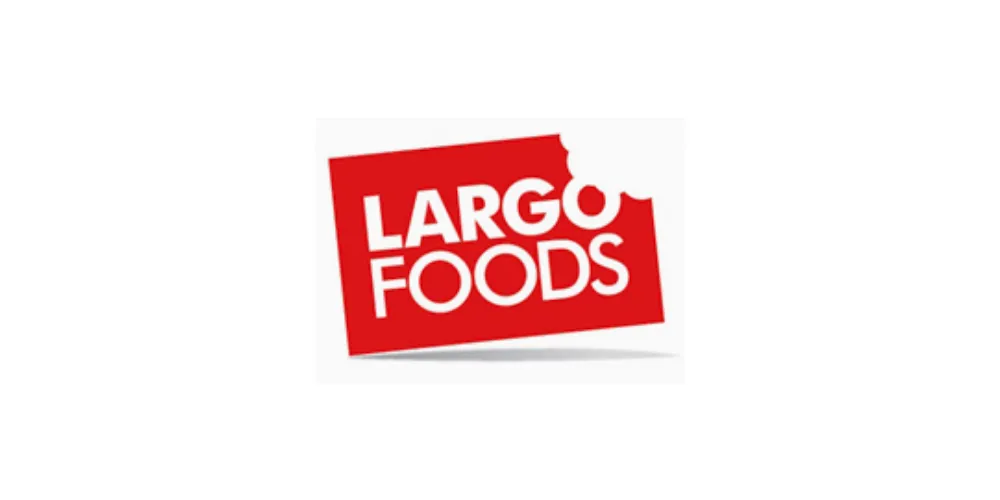
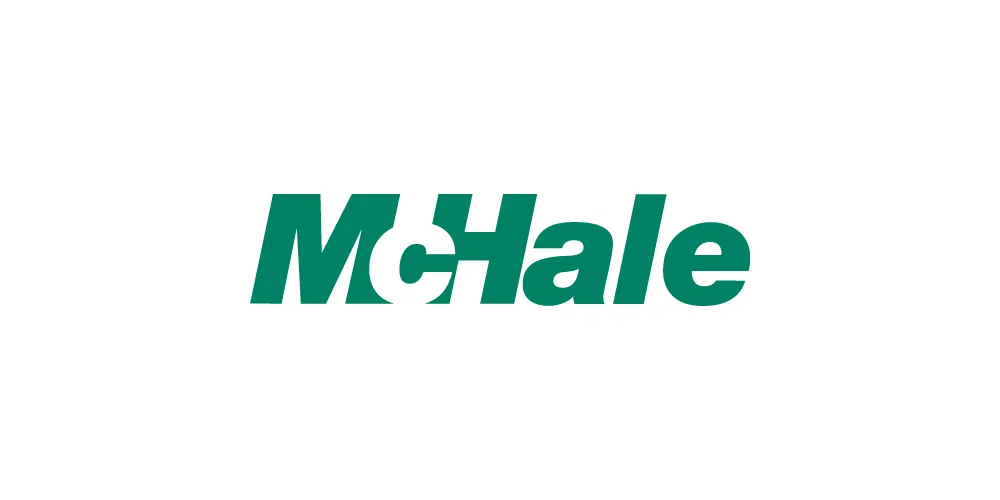
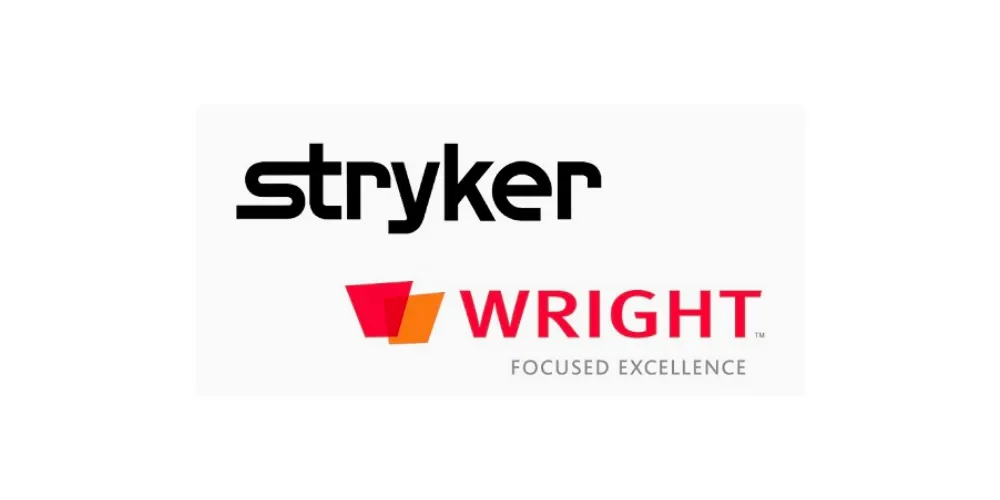
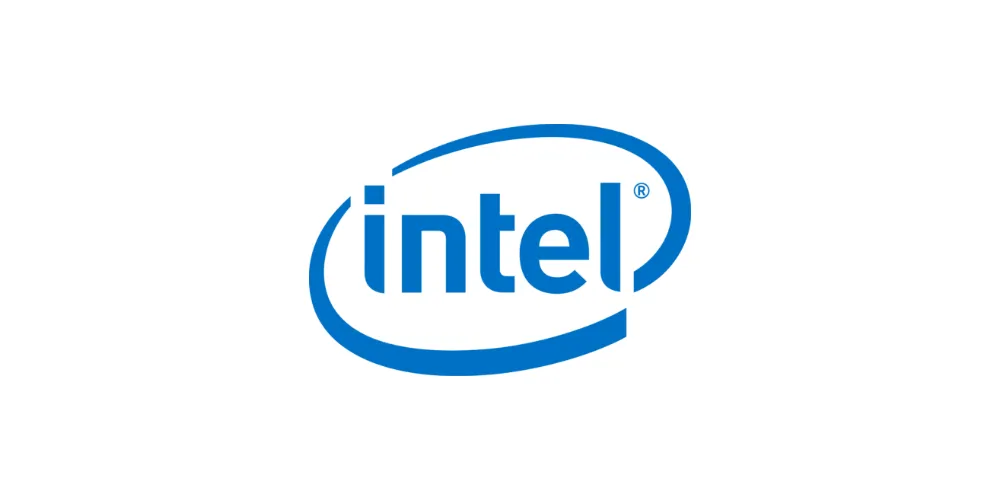
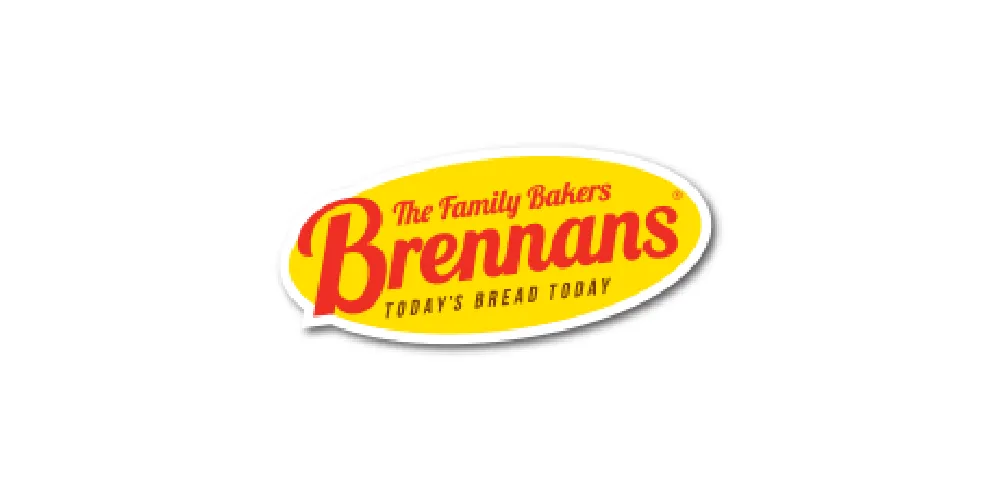
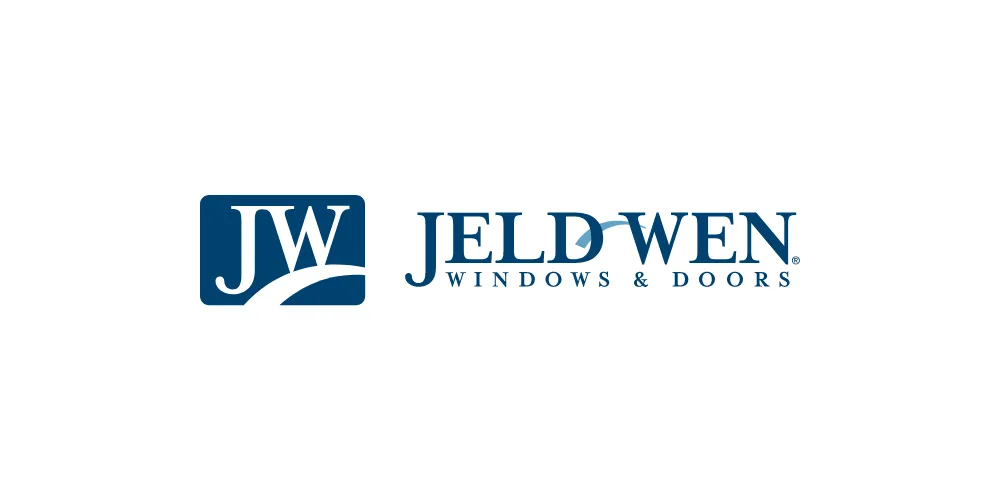
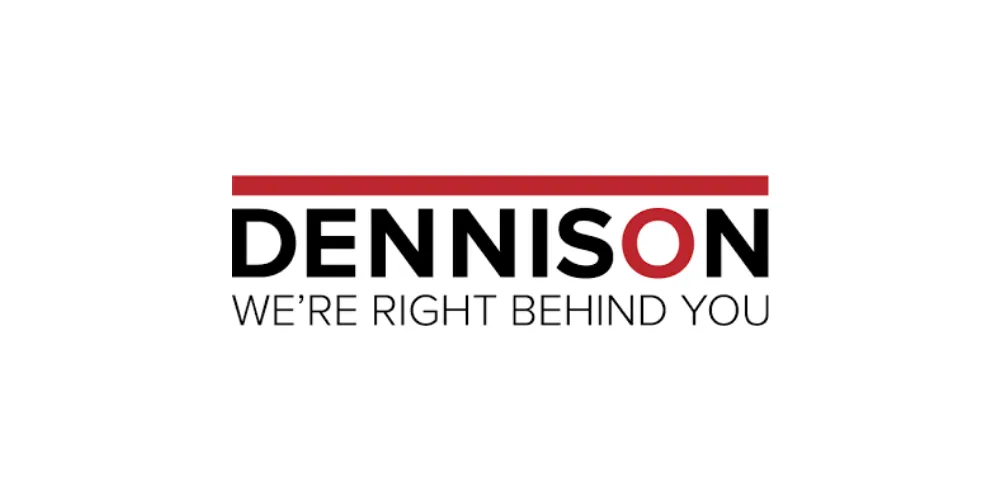
Too Busy Right Now?
We can send you a reminder to have a consultation later