“SeaChange has shown us the importance in connecting our people to process and making safety a personal issue. We are excited to continue our work and development with SeaChange and their lean, sustainable approach.”
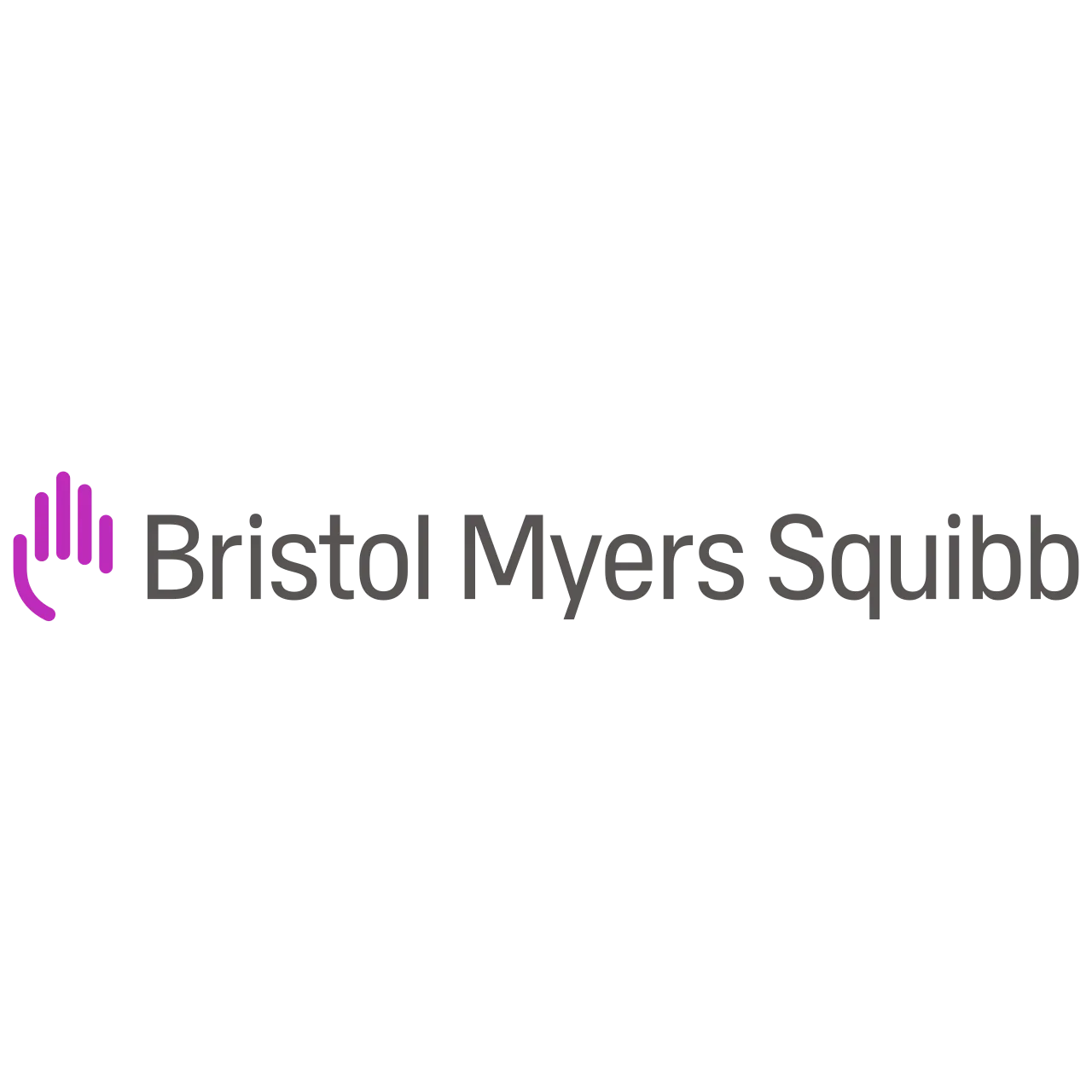
Bristol Myers Squibb Swords
Safety Culture Transformation Programme through SeaChange leads to Pharma Industry Safety Award for Bristol Myers Squibb Swords
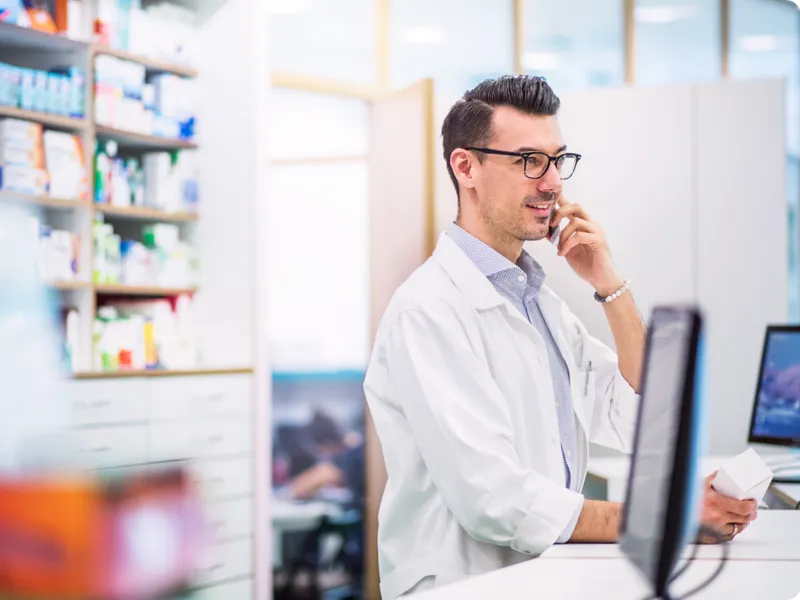
Client Profile
Bristol Myers Squibb is a global Bio-Pharma company firmly focused on its mission to discover, develop and deliver innovative medicines that help patients prevail over serious diseases.
Around the world, our medicines help millions of people in their fight against such diseases as cancer, cardiovascular disease, diabetes, hepatitis, HIV/AIDS, rheumatoid arthritis and psychiatric disorders. BMS’ manufacturing operations in Ireland include one Active Pharmaceutical Ingredient (API) site in Swords, Co. Dublin, and the current development of a new Biologics facility on its legacy API manufacturing site in Cruiserath, Co. Dublin.
The Challenge
At Bristol Myers Squibb (BMS) Swords, people are at the heart of everything and there is a strong commitment to creating a safe and positive work experience. The site is over 50 years old and many personnel have worked at BMS for their entire career, leading to a culture of community, based on friendship and family. Given the high-risk nature of the work that is carried out at the site on a daily basis, Safety is a priority. BMS Swords has a recognised robust Safety Management System (SMS), based on a multifaceted approach.

Unfortunately, even with this comprehensive and continually improving SMS in place, injuries were still experienced at BMS Swords. The senior leadership team recognised that a shift in people’s mindsets was required to improve safety standards, accountability for safety and, in particular, safety behaviours. The tipping point had been reached; Safety Culture Evolution through Behavioural Safety improvements became the key safety focus at BMS Swords in 2016 and beyond.
While benefits from initiatives like the DuPont STOP for Supervision™ (SFS) were realised, some key challenges associated with these initiatives were also encountered, forming the need for a different kind of intervention. The decision was made to drive a transformational cultural evolution in terms of onsite safety because, although numerous major safety initiatives had been introduced to complement excellent existing systems, it was felt deep down that ‘something was missing’.
The Solution
Through extensive and collaborative work with Safety Culture experts, SeaChange, BMS Swords found the missing piece – a sustainable behaviour-based solution that works from the ground up: the BMS-SeaChange Safety Culture Transformation Programme.
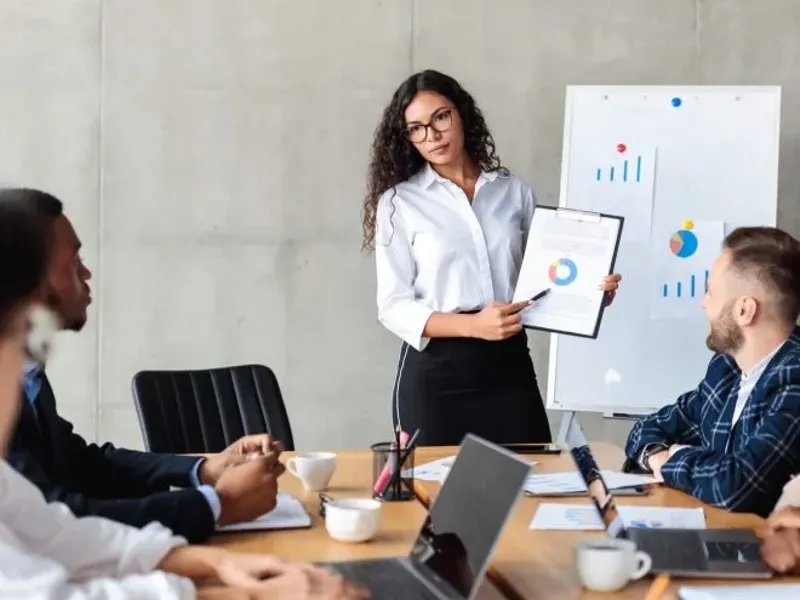
This collaboration has been the catalyst towards deep and lasting positive growth in Safety Culture at BMS Swords, facilitating a stepped change through Stages 2 to 3 to 4 on the Bradley Curve in a sustained way from the ground up, building Accountable behaviours and attitudes that support success.
This Safety Culture Initiative was initially focused on driving operational improvement through managing risk sustainably — specifically, effectively connecting ‘people & behaviour’ to the Safety message, sitewide. Starting any lean process in a large manufacturing facility requires accurate identification of current operational safety culture gaps; in this instance, gaps were identified and analysed through the SeaChange Safety Culture Footprint process at the operations, frontline management and senior management levels.
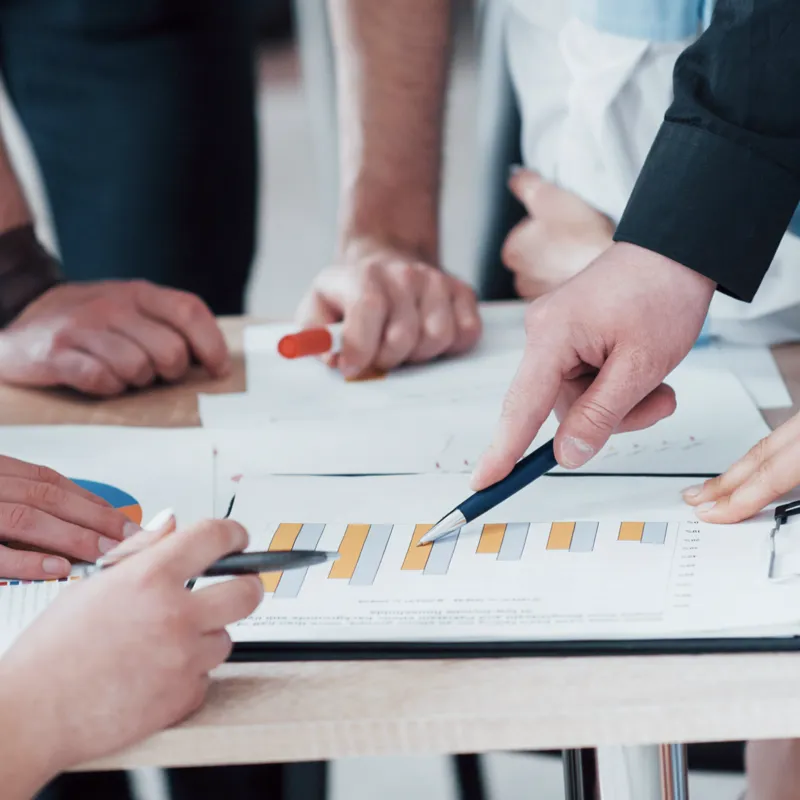
Phase 1: Measure Safety Culture to Identify Gaps
The first phase in the BMS-SeaChange Safety Culture Transformation Programme was for SeaChange to accurately measure safety culture onsite and identify the behavioural and cultural gaps that needed to be addressed. SeaChange completed Safety Culture Footprint workshops with a 20% sampling of the workforce across all levels within the organisation. These engaging workshops enabled SeaChange to gather and analyse valuable information on the prevalent attitudes, behaviours and operator frustrations that were creating the lack of ownership for safety on the ground.
The Safety Culture Footprint process resulted in a Management Report that pointed to specific attitudes and behaviours that were restricting people from taking ownership of health and safety in BMS Swords. The report reflected the full spectrum of latent attitudes leading to unsafe behaviours and informed BMS’s 2016 Safety Culture Evolution Roadmap. The main objective was to prioritise strategic actions to increase safety ownership at operations, management and senior management levels, and to take key steps for continuous and sustainable operational improvement in 2016 and beyond.
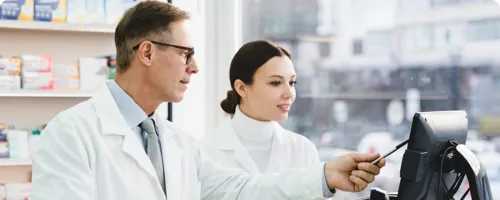
Phase 2: Implement a Safety Ownership System
The second phase in the BMS-SeaChange Safety Culture Transformation Programme was to implement a bespoke, behaviour-based solution that would increase personal accountability and staff ownership from the ground up. Building on learnings from the Safety Culture Footprint, the BMS-SeaChange Safety Culture Initiative introduced the SeaChange Safety Ownership System, which has been key to driving behavioural change on the operational floor.

As part of the SeaChange Safety Ownership System, Safety Action Teams (SAT©) were set up on a phased basis in critical operational zones on the BMS Swords site. Interactive SAT Displays provided a focal point and Visual Contract for safety in each area and enabled a mechanism whereby local risks could be prioritised and recorded by those working in the area. Consequently, the actions and outcomes pertaining to each risk are locally agreed upon and owned. Routines for SAT Teams were introduced to ensure the sustainability of the growing culture of safety ownership. These routines established a best-practice language for all. Clearly defined roles and responsibilities for SAT Team members and recurring meetings, reviews and deliverables ensured that the system could run continually.
The whole initiative was connected seamlessly into existing processes, such as Tier Process and GEMBA, thus preventing any potential conflicts of interest. SAT Routines have continued to build and promote local buy-in, accountability and ownership, and there is a palpable sense of a strong Safety Culture emerging across critical areas onsite.
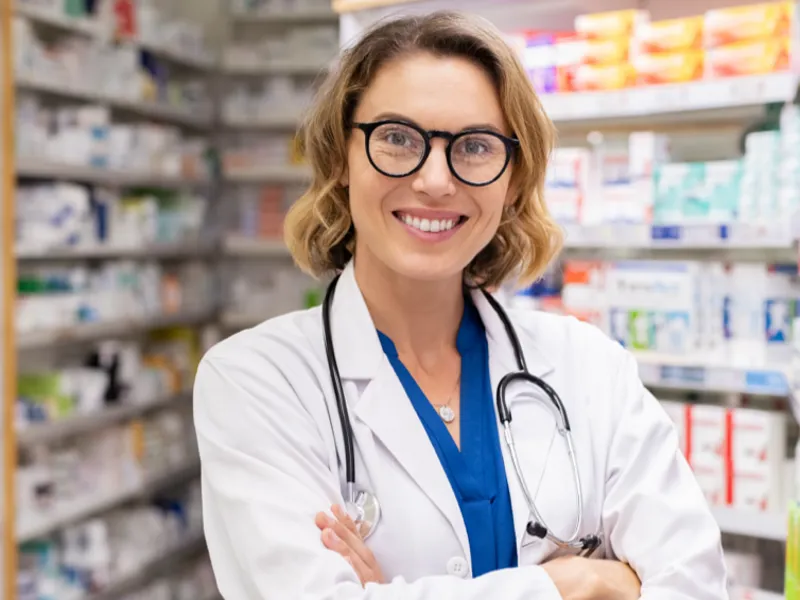
Phase 3: Leading Safety Culture in a Sustainable Way
The third phase of the BMS-SeaChange Safety Culture Transformation Programme was to coach safety leaders onsite to foster a positive safety culture in a sustainable way. A Senior Team and Frontline Management Coaching Programme was implemented through SeaChange to support the Safety Culture Evolution.
The objective was to enable consistent delivery throughout the initiative while ensuring sustainability over the long term through effective leadership. The Coaching Programme encouraged and influenced BMS management to continuously drive and lead the Safety Culture Evolution onsite and those involved responded exceedingly well to it. The result was a palpable improvement in safety communication, management and leadership across the site.
The Results
To date, there has been a huge shift in BMS Swords, from apathy and frustration to people feeling connected and taking ownership of local EHS best-practice behaviours. The workforce is getting involved and making a difference; the Safety Culture in BMS Swords has significantly evolved.
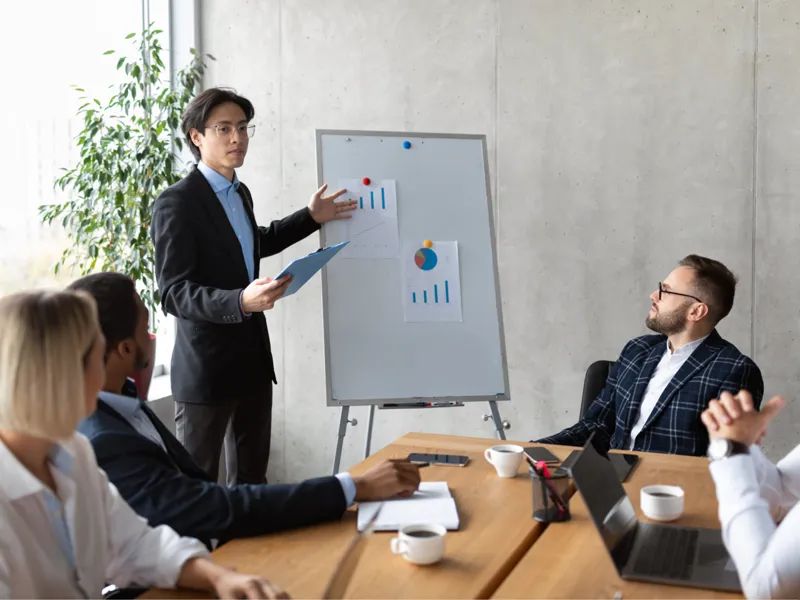
Safety is an evident priority on the operational floor, through visual tools and the resulting behavioural changes within the empowered workforce. At BMS Swords, the Safety Culture has moved from a reactive response to a proactive approach that not only manages risk but promotes safe behaviours through inter-dependent teams.
Since introducing SeaChange to improve their Safety Culture through a bespoke programme, Bristol Myers Squibb Swords have seen the following ground-breaking results:
-
93% increase in workforce engagement
-
600% increase in management safety walkabouts
-
52% increase in near miss reporting
-
78% decrease in injury reduction
In addition, this transformative safety culture initiative led to Bristol Myers Squibb Swords winning the Pharma Industry H&S Award in 2016. These market-leading results are clear indicators that Bristol Myers Squibb Swords found the missing piece in building a sustainable safety culture – SeaChange.
Mary Moran | Director, BMS Swords API
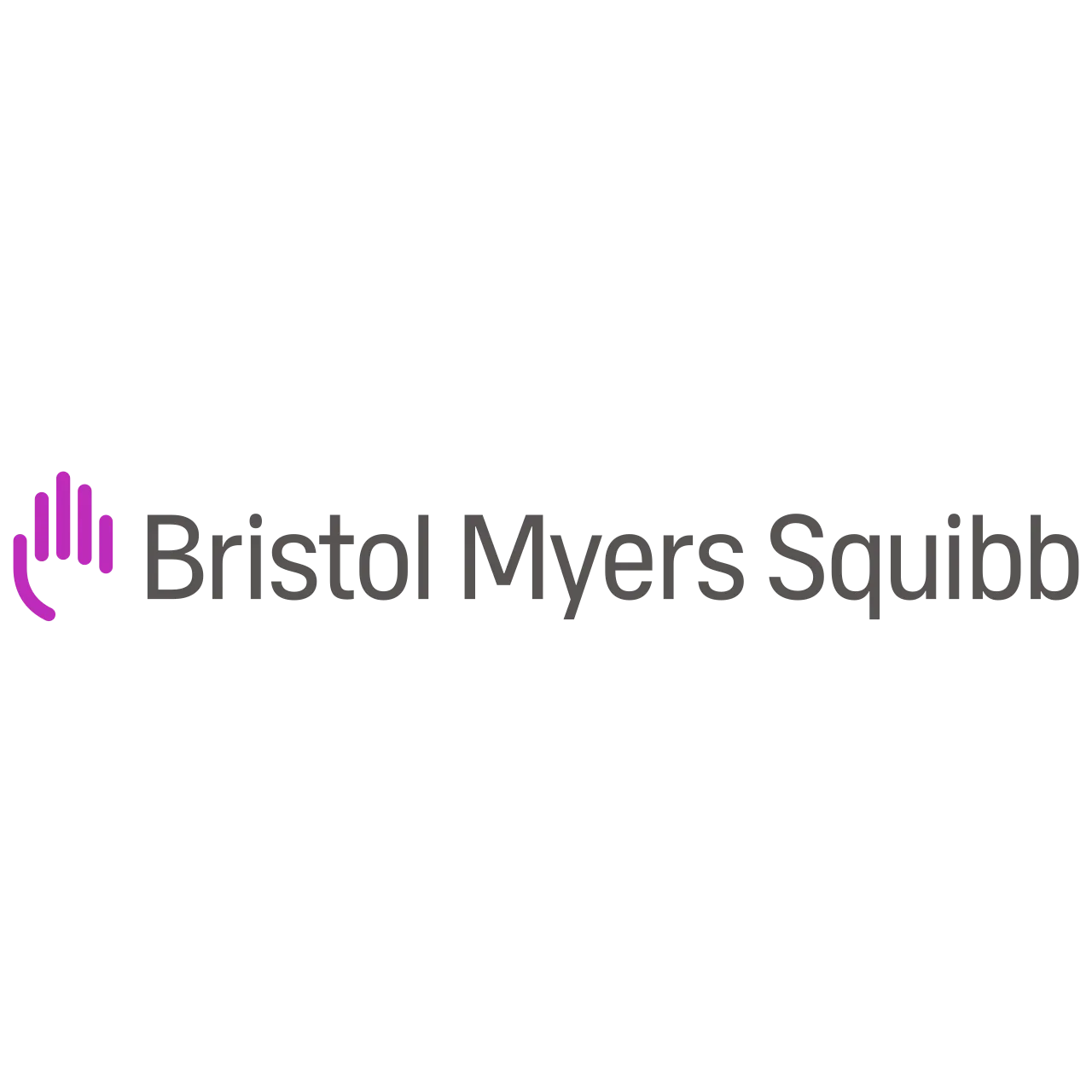
It is critically important for all of our site colleagues to take a personal role in their safety and that of their colleagues. I witnessed first-hand how the Safety Ownership System engaged our shop floor colleagues in the design and implementation of the local SAT™ teams. The passion and enthusiasm that was displayed during the design phase will certainly ensure that we are successful in driving a culture of safety.
Andrew Espejo | General Manager, BMS Swords API
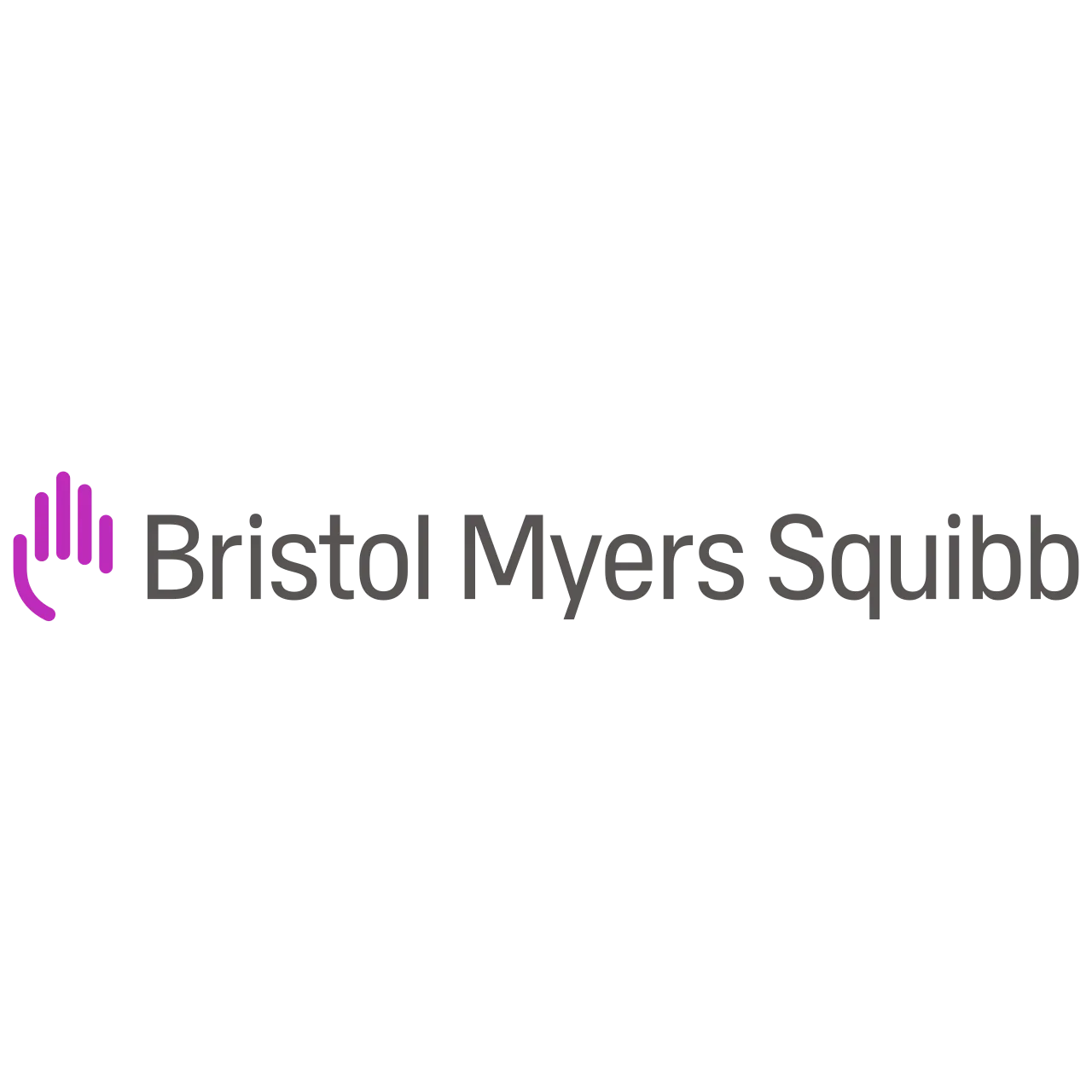
“I feel that this is the first time we have been treated this way – with openness, honesty and a real chance to be involved in what really matters – our safety. I am seeing a very positive change in how we do things around here when it comes to safety. I’ve been here 30 years and I have to say there are a lot of legacy issues that need to be dealt with. Now that we measured our culture and have set up the Safety Ownership System throughout the plant, I can really see a major change, we are working on safety priorities and seeing commitment from the company to supporting major changes where needed.’’
Large Scale Plant Chemical Process Operator | BMS Swords API
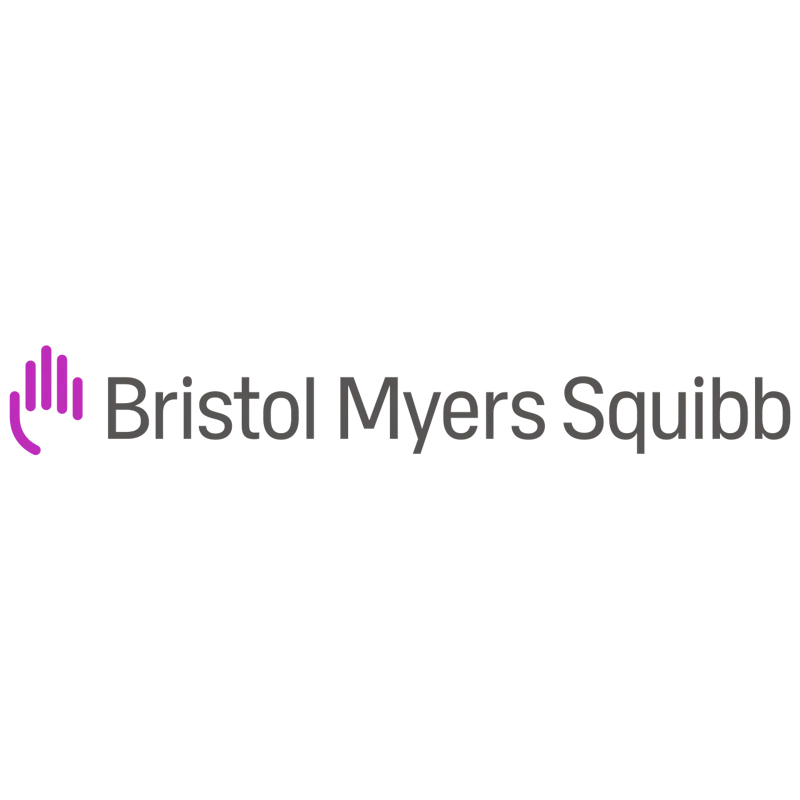
Case Studies
Too Busy Right Now?
We can send you a reminder to have a consultation later