“SeaChange understand people, behaviours and lean management. They have developed leading edge solutions and tools that positively impact attitude, behaviours and results at every layer in our business. We began working with SeaChange to try and improve our safety culture. We immediately experienced both tangible results (reduced accident rate by 75%) and intangible results (improvement in staff morale). Their systems are very visual and simple to monitor, allowing structured training of all operators and auditing of the safety controls. Their systems also fit well with Lean and World Class Warehousing. We are now working with SeaChange on a number of lean management projects and leadership training to continue to grow our overall culture in the right direction”.
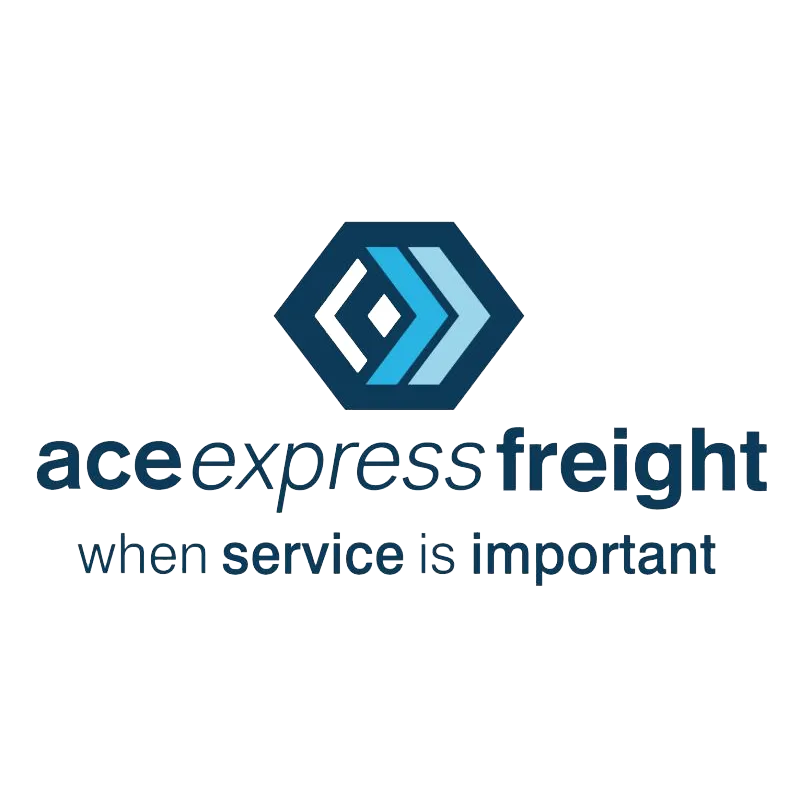
Ace Express Freight
Accidents and Incidents led to a ‘SeaChange’ in Safety Systems and Safety Performance at Ace Express Freight
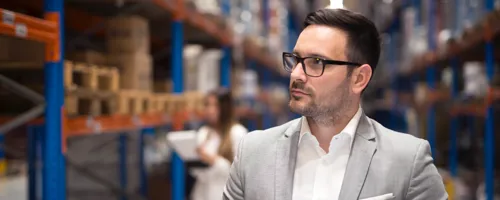
Client Profile
Ace Express Freight is one of the leading family-owned freight and logistics companies in Ireland, with over 30 years of experience, a team of 160 staff and contractors, a nationwide distribution network in Ireland and the UK, and a global partner network spanning 173 countries.
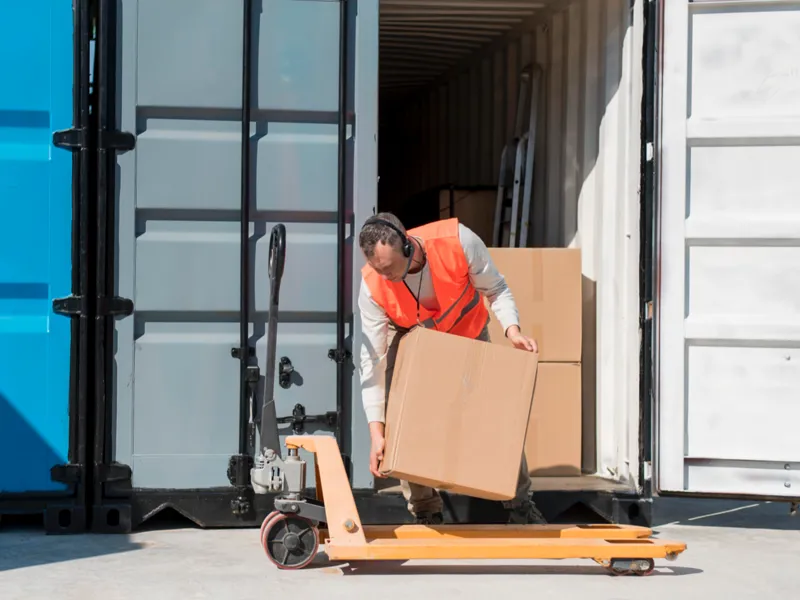
The Challenge
As CEO and owner of Ace Express Freight, a number of accidents to personnel led Philip Tracey to carry out a root and branch study of the company’s safety systems, with a view to a step change improvement being needed in safety performance.
The study showed that whilst the company was covered from a legal standpoint, there was a real disconnect between the safety policy and risk assessments sitting on the managers’ shelves and what was actually happening in practice in the warehousing and distribution areas.
The Solution
After much research on how best to fill this deficit, Ace Express Freight engaged the services of SeaChange to help assess the organisation’s existing safety culture and implement systems to improve their safety performance.
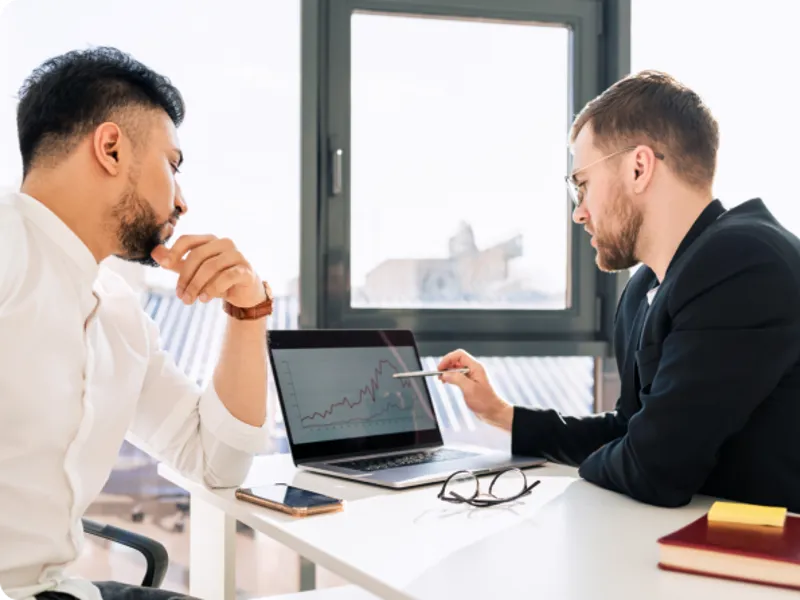
Phase 1: Measure Safety Culture to Identify Gaps
Through a Safety Gap Analysis, SeaChange accurately measured safety culture onsite to identify the behavioural safety gaps that need attention. After conducting a safety gap analysis, SeaChange completed Safety Culture Footprint workshops with a 20% sampling of the workforce across all levels within the organisation. The Safety Culture Footprint process resulted in a report that accurately measured Safety Culture, and the Safety Gap Analysis prioritised the key actions required to make immediate safety performance improvements.
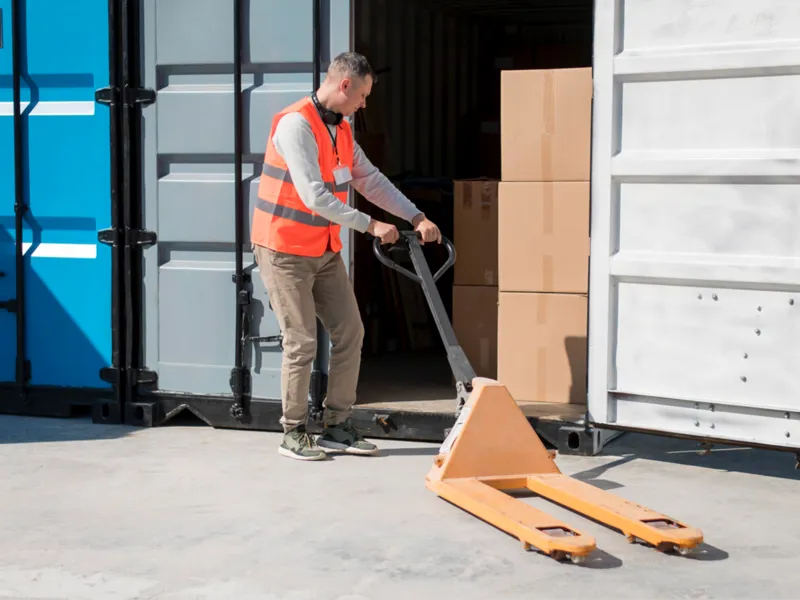
Phase 2: Implement Safety Systems
SeaChange then implemented a behaviour-based safety solution that would help to connect staff behaviours with the organisation’s safety standards. SeaChange introduced two systems into Ace Express Freight:
Risk Awareness System
This system enabled Ace Express Freight to engage with their workforce and create visual safety standards, known as Job Safety Awareness (JSA©) visuals for local areas of operation throughout the business. These visual tools helped to animate risk, hazards and controls while also ensuring that the workforce was trained and refreshed in key safety standards. This system served to bring ‘safety to life’ in all areas of the business and connect standards with people.
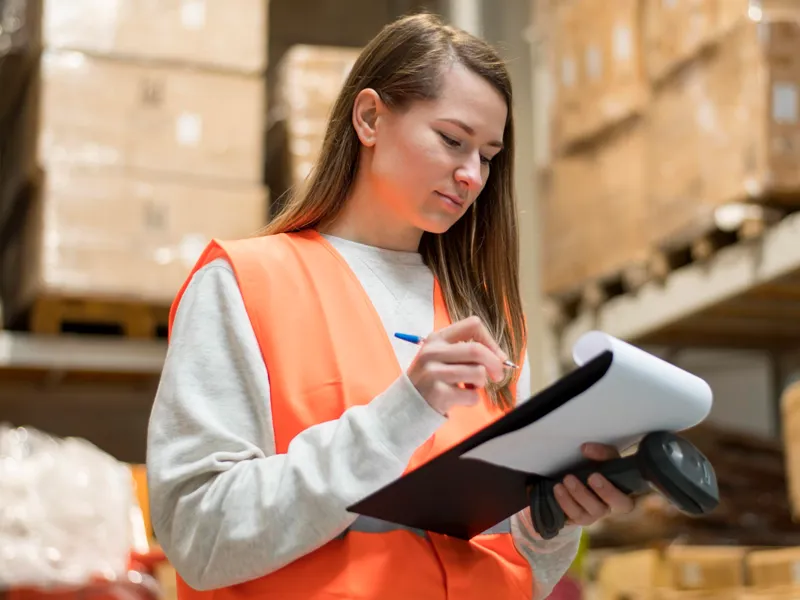
Safety Ownership System
This system was introduced to improve local safety ownership through effective risk prioritisation and safety actions across the business. Safety Action Teams (SAT©) were established across numerous zones throughout the Ace Freight operation. These SAT teams managed the risk priorities across shift patterns in their local area through an interactive SAT display in each zone. Local SAT teams included operators, a team leader and the front line managers, with each person playing a part in identifying risk priorities and actioning safety behaviours. This key process began rebuilding safety culture from the ground up.
The Result
Following the initial safety culture measure and subsequent implementation of SeaChange systems at Ace Express Freight, there was an immediate rise in employee awareness and engagement with general safety and the safety message.
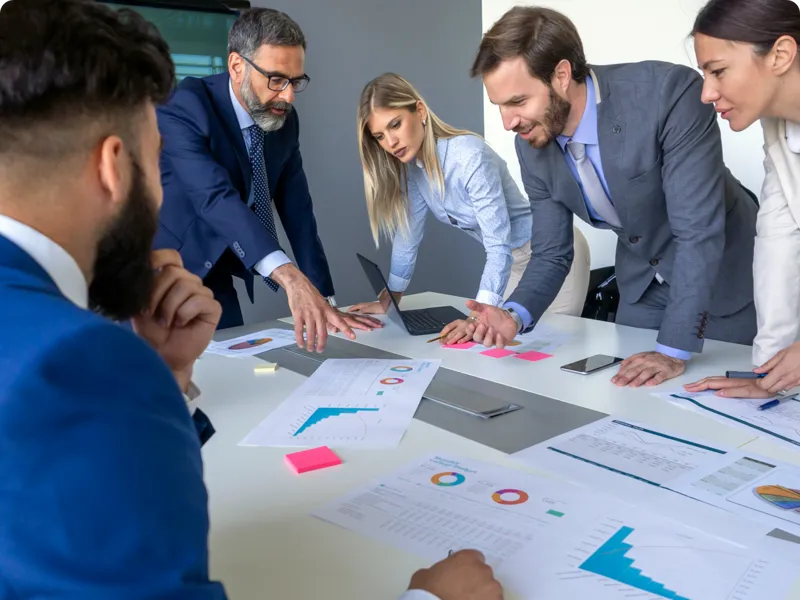
It was evident that the SeaChange Safety Ownership System generated local ownership and personal accountability, and over time safe practices, habits and behaviours became second nature across the business.
Along with reductions in accidents and incidents, productivity and morale increased as a result of the unique SeaChange approach and people-based systems. Since introducing SeaChange to improve their Safety Culture, Ace Express Freight have seen:
-
63% increase in local safety correctives
-
82% increase in operator risk awareness and training
-
75% decrease in lost time incidents
Philip Tracey | CEO and Owner – Ace Express Freight
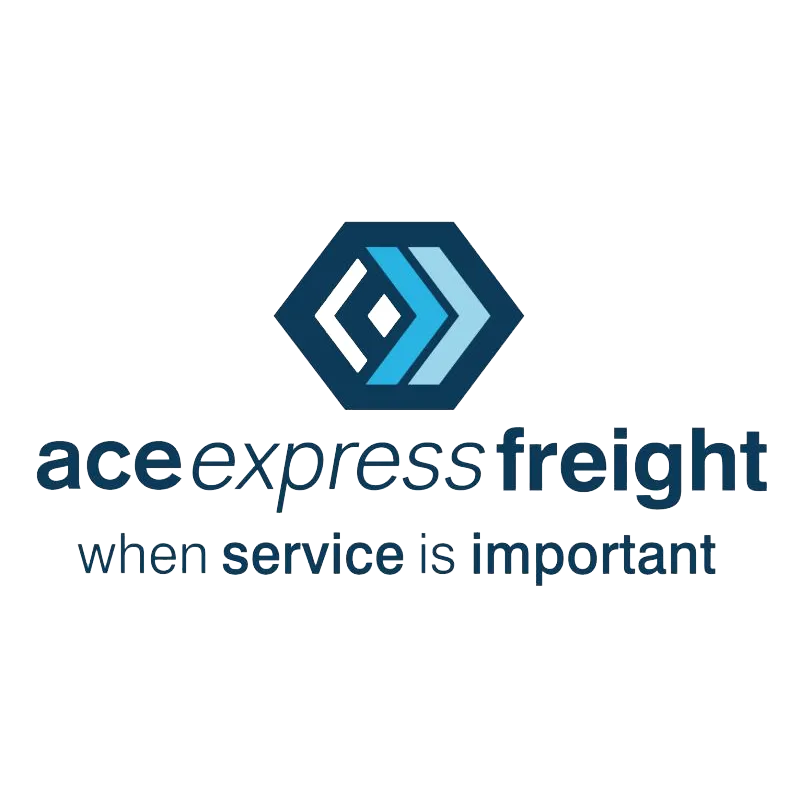
Case Studies
Trusted By
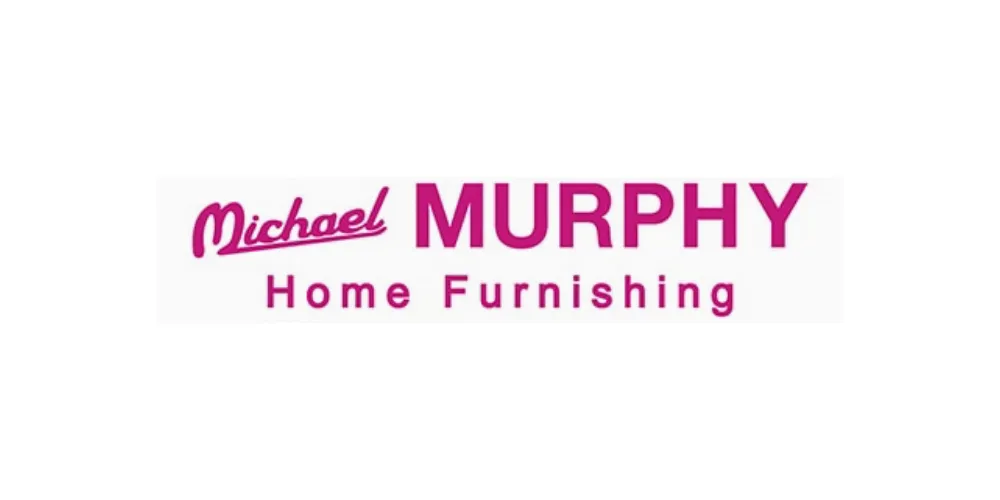
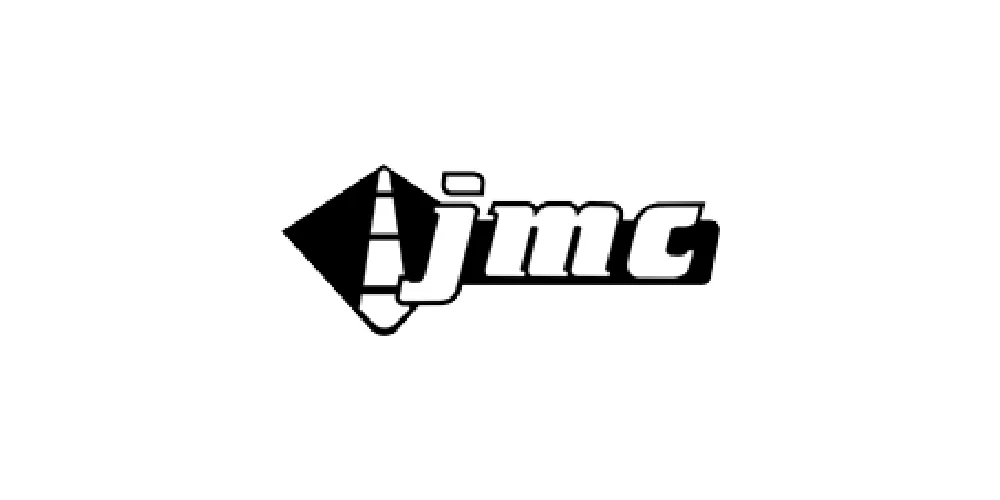
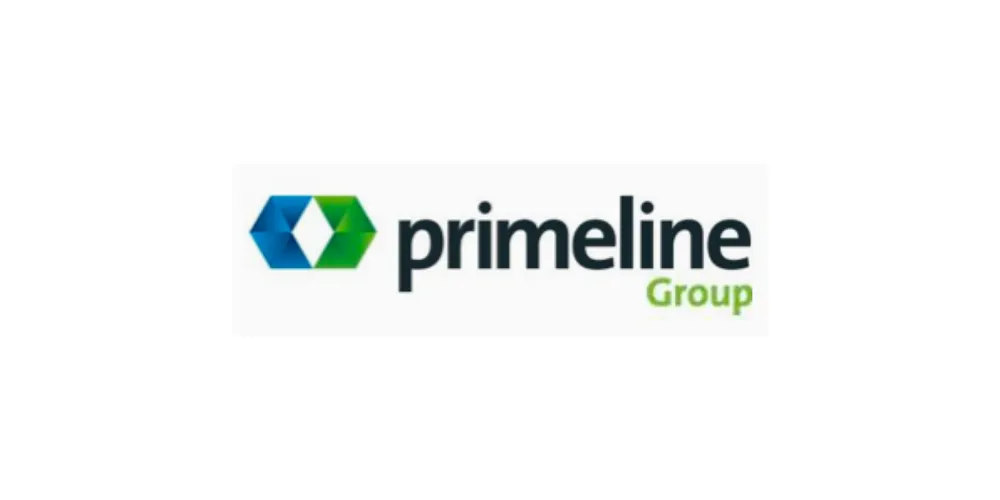
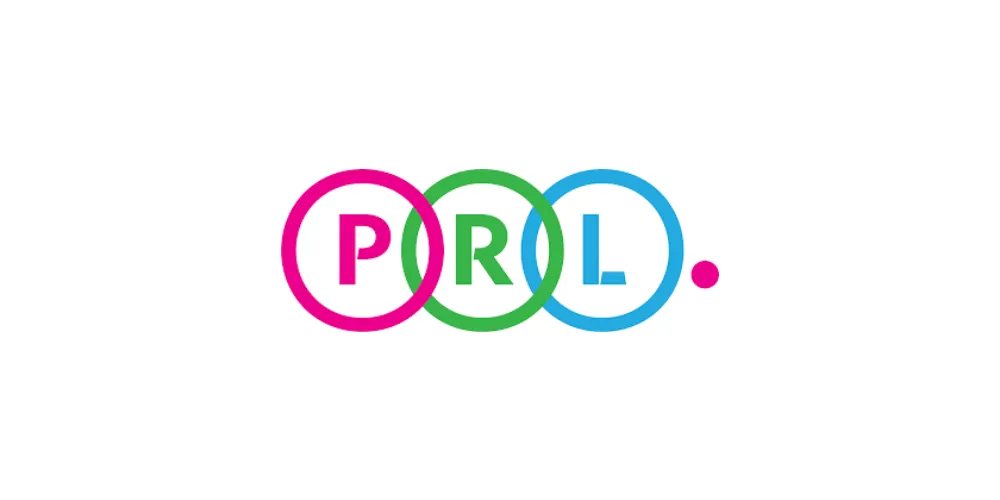
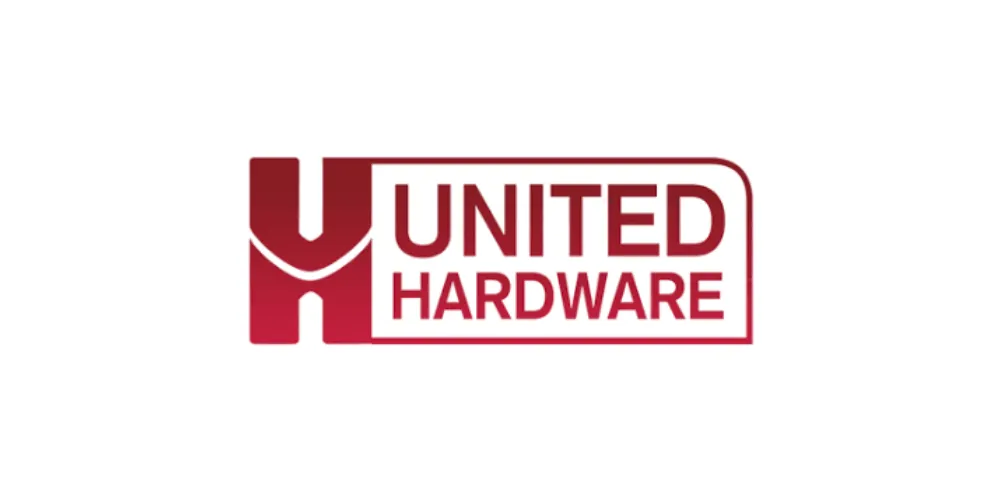
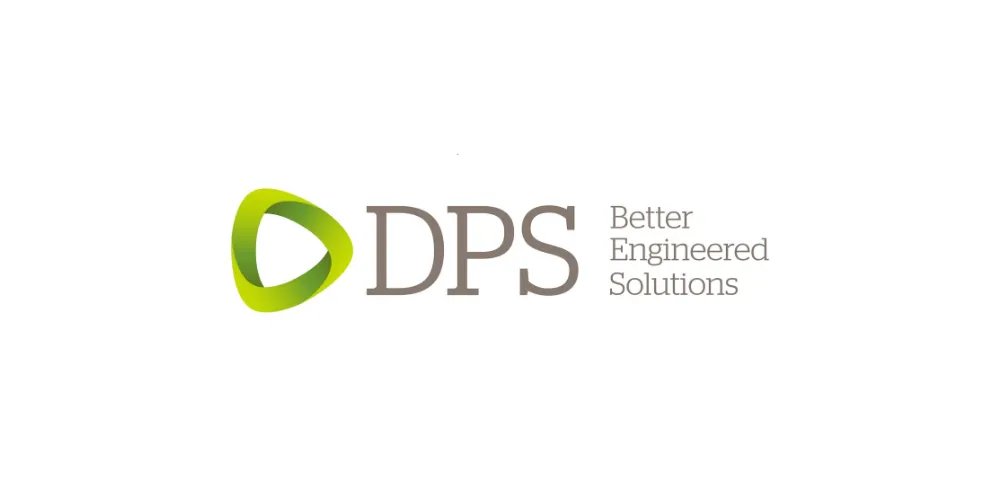
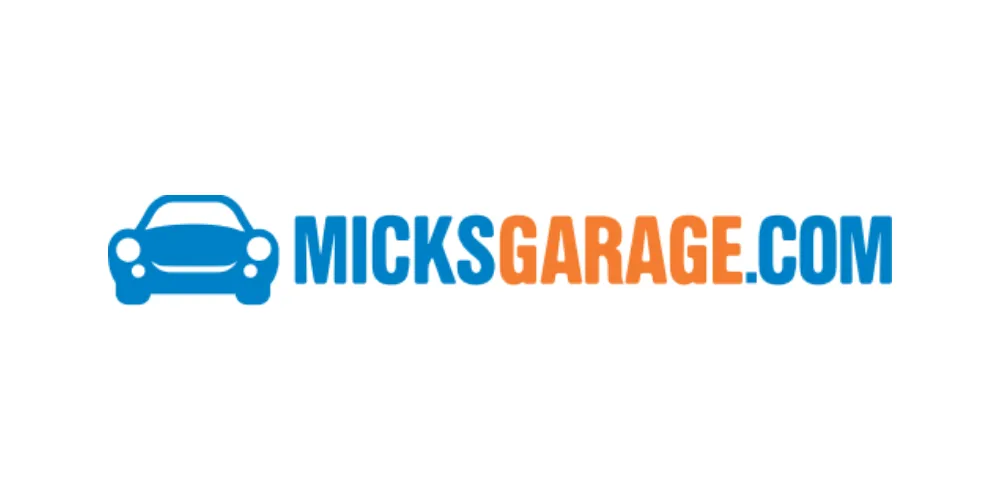
Too Busy Right Now?
We can send you a reminder to have a consultation later